
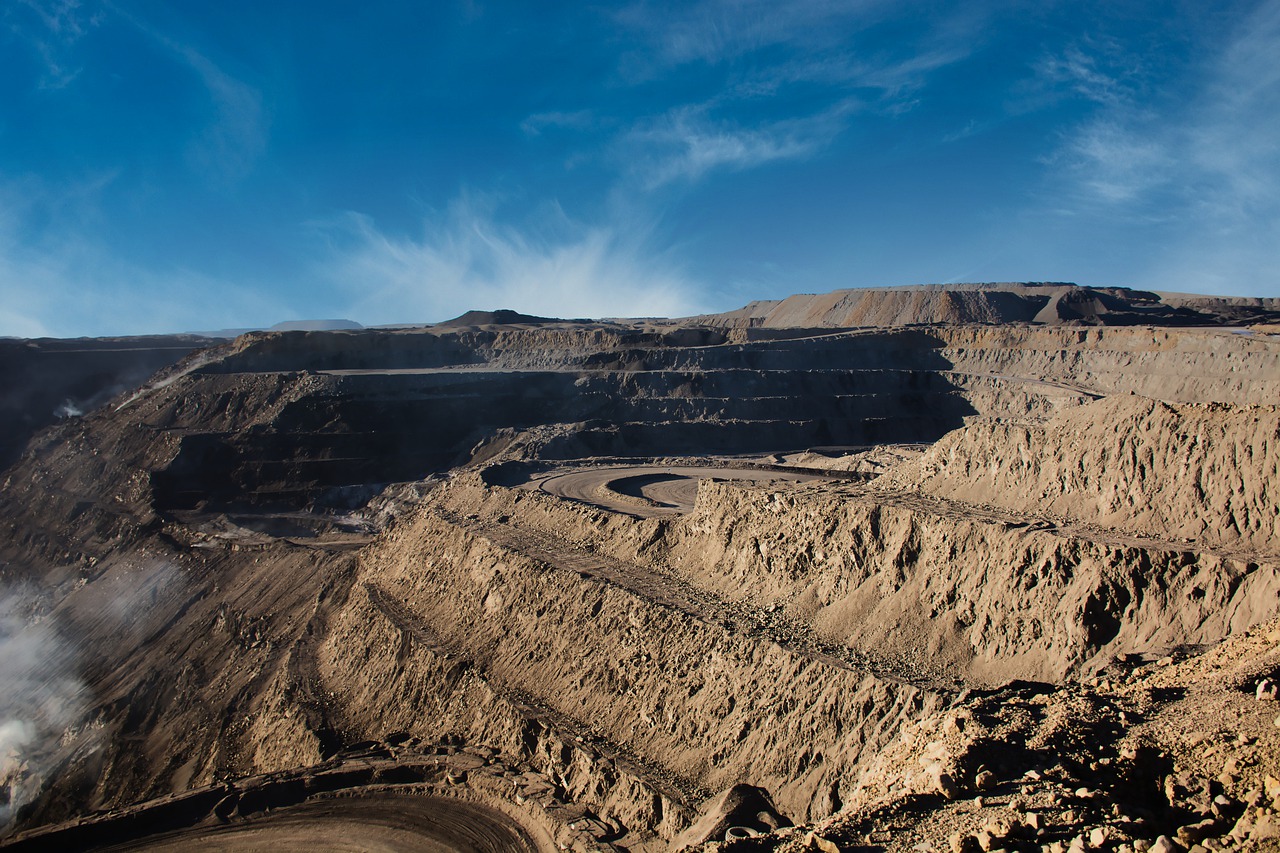
Case Study 1
DATE:
10/5/2019
ISSUE:
Truck 514, position 2 (left front) was continuously overheating
NOTIFICATION:
The issue was brought to attention due to the temp delta on the daily report.
ACTION:
The maintenance crew inspected the truck and found that the heat shield on the right side of the radiator was completely missing.
WIN:
The info provided allowed the mine to order the correct parts and resolve the problem. Position 2 no longer overheats
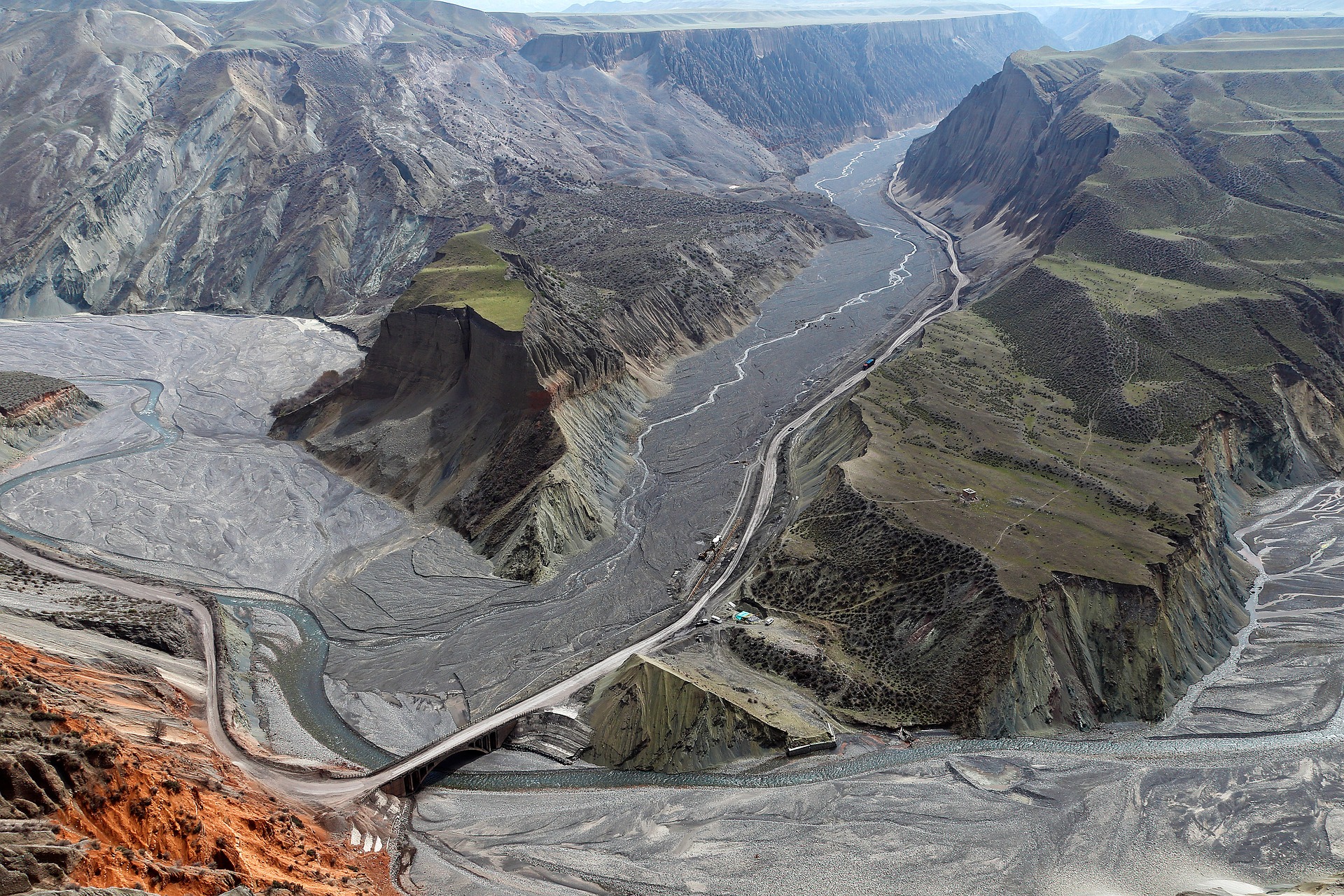
Case Study 2
DATE:
9/5/2019
ISSUE:
Based on the Lat acceleration map, Bridgestone iTrack picked up on inconsistencies on the road
NOTIFICATION:
The user noticed in WebTrack that on a particular route there was a lot of side to side movement and g-forces on the trucks.
ACTION:
The user went out in the pit and found two corners that had negative super elevations. She had them corrected.
WIN:
Not exceeding lateral force of what engineering would recommend for the tire. By correcting the curves, the tires are no longer exceeding the later force and flex they were designed for which prevents early wear and premature failure.
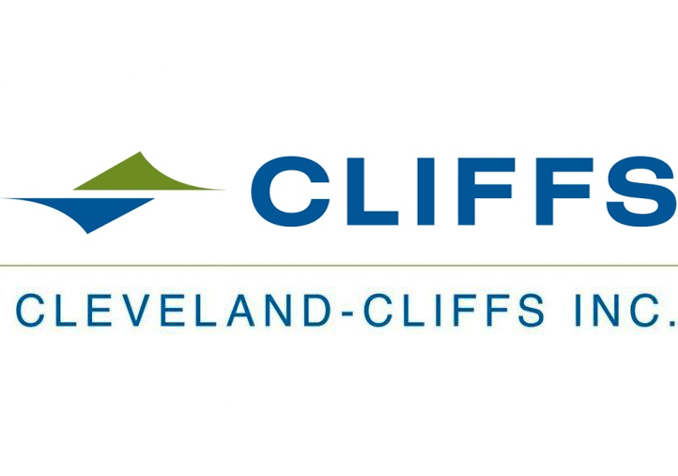
Case Study 3
DATE:
10/7/2019
ISSUE:
Truck 531 had a level 3 temp alert on P2, it reached 183 F at its max (level 3 is set at 180). P1 was following closely behind at 176 F.
NOTIFICATION:
The user, the head tire fitter, saw the issue on WebTrack and received an e-mail alert
ACTION:
The user called the mine operations and asked them to move the truck to a shorter haul (not park it)
WIN:
Temperatures in both positions came down. This is an ideal scenario as it keeps the vehicle in operation while dealing with the issue at the same time.
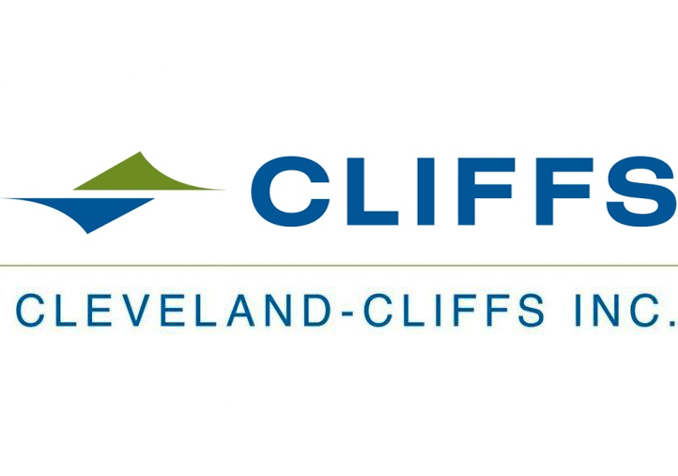
Case Study 4
DATE:
14/7/2019
ISSUE:
The monitoring center picks up on a slow leak on Truck 535, position 3 (outside rear).
NOTIFICATION:
The mine was alerted via an e-mail alert
ACTION:
The tire maintenance crew was able to pick this up from the alerts generated by the system and stop and inspect the truck at which point a cut in the sidewall was found.
WIN:
The tire was replaced and the truck returned to operation. Picking up issues such as this on rear tires is important as it increases the chance the damaged tire can be repaired and also prevents causing damage to the outside inner tire (P4) as they run as a pair.
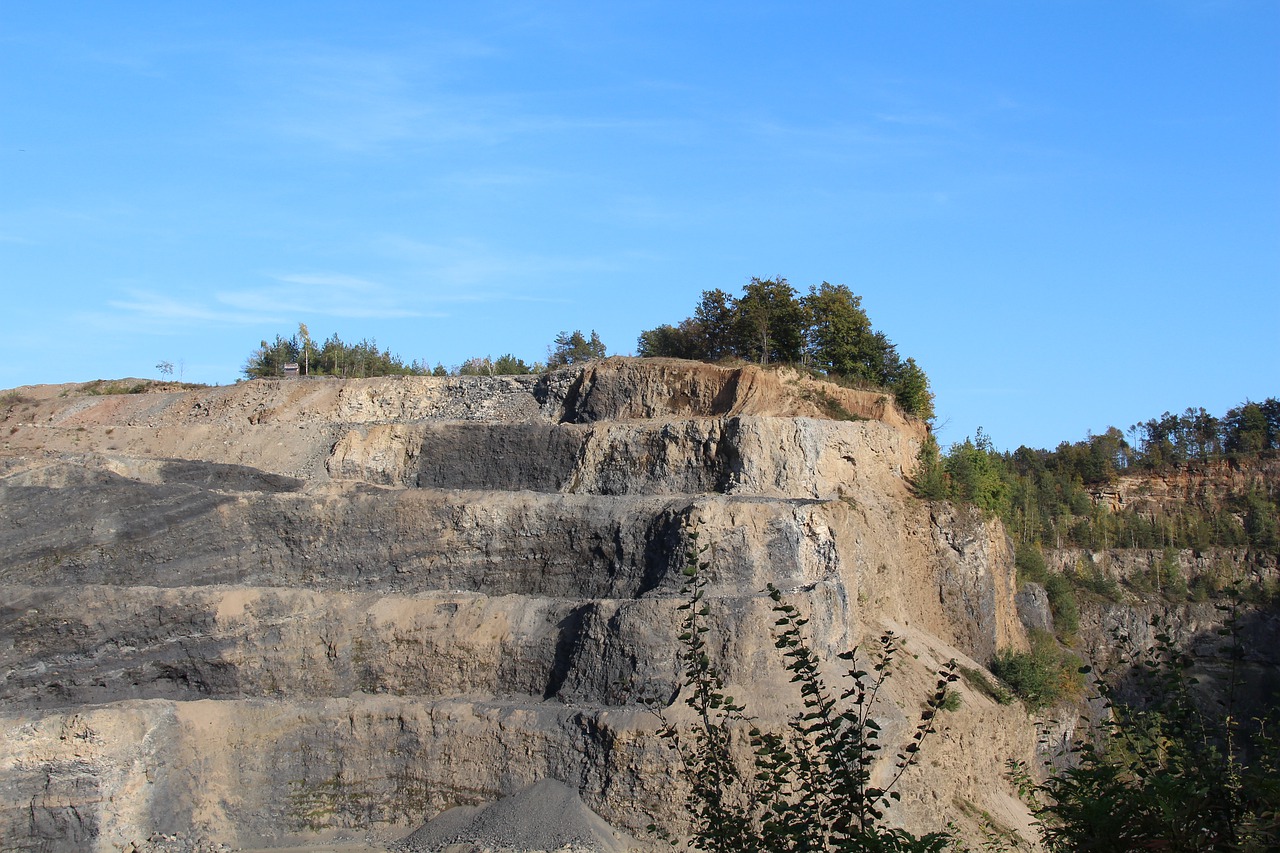
Case Study 5
DATE:
—
ISSUE:
The mine stated that 4 tires were saved. The company confirmed that 6 tires were saved because the dual tires were also saved, totaling ~$180K in savings or ~$30K per tire. (3 vehicles for all 6 tires)
NOTIFICATION:
Speed related issues being brought to the forefront to work on operator behaviors.
ACTION:
—
WIN:
16 out-of-service tires in 9-11-2019 inspection did not have any heat-related issues due to excessive TMPH since Bridgestone iTrack being installed.
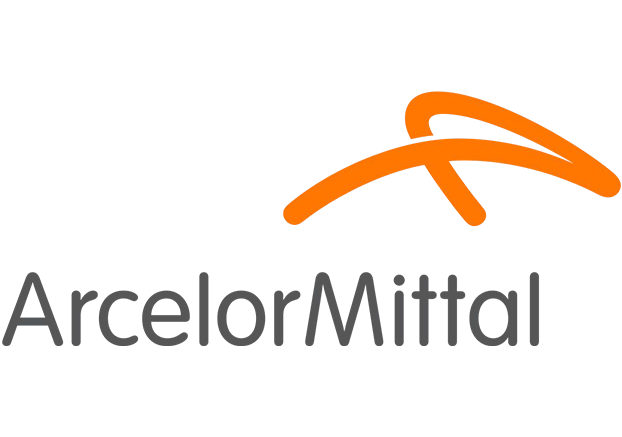
Case Study 6
DATE:
10/5/2019
ISSUE:
Bridgestone iTrack picked up a potential mechanical issue by monitoring the temperature delta of the 2 front tires
NOTIFICATION:
Bridgestone iTrack flagged the truck and informed the customer to inspect. This is reported on the daily dashboard report that is sent out to the customer each morning
ACTION:
An order was put in for the truck to be checked during PM for a tweaked frame and strut pressures on the next fuel top off. Bad right front strut confirmed and changed out.
WIN:
Picking up this issue in advance prevents major damage to the truck and lengthy downtime. Tires are more susceptible to cuts and premature wear which could result in shorter tire life by 25%-50% for multiple tires until the problem resolved.
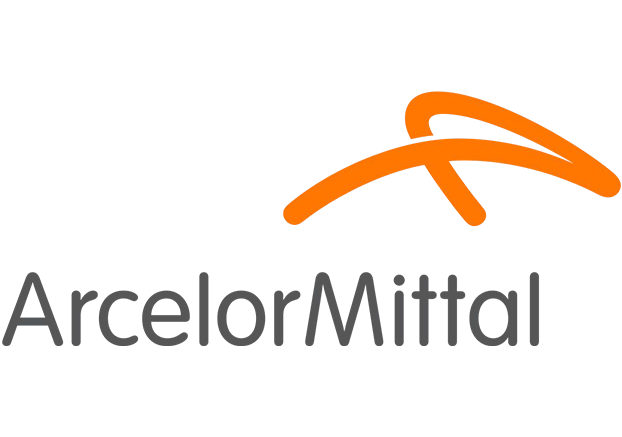
Case Study 7
DATE:
10/9/2019
ISSUE:
Downtime changing to different tire compounds for different seasons
NOTIFICATION:
The alerts and reports generated from the Bridgestone iTrack system confirmed that tire temperatures were running lower than anticipated.
ACTION:
This will likely enable the mine to run E2A compound tires year-round. The mine plans to test this on a sample of vehicles before rolling out to the remaining fleet.
WIN:
Could move heat resistant tires to scrub resistant tires year-round. This results in ~15%* better tire wear and less downtime changing tires out to E1A on the fronts as the weather warms up in the spring.
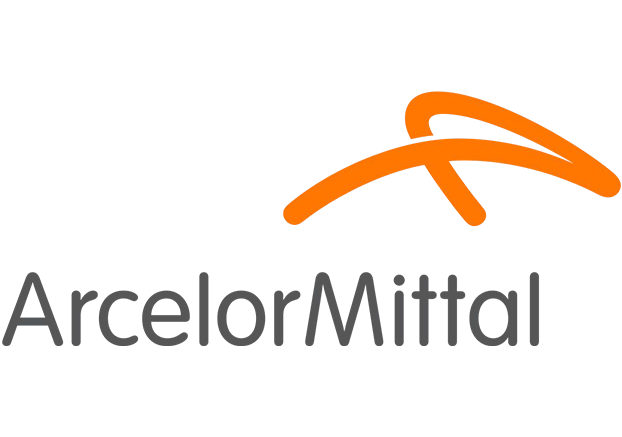
Case Study 8
DATE:
26/11/2019
ISSUE:
Truck T204 had a pressure leak in position 4, the tire reached a level 3 alert
NOTIFICATION:
The Bridgestone iTrack system sent an e-mail and recommended that the tire be inspected and take the recommended corrective action.
ACTION:
The user confirmed that they did end up changing this tire on 11/27/2019 and that it was detected prior to the daily fuel bay checks
WIN:
The tire was replaced and the truck returned to operation. Picking up issues such as this on rear tires is important as it increases the chance the damaged tire can be repaired and also prevents causing damage to the dual tire (P3) as they run as a pair.
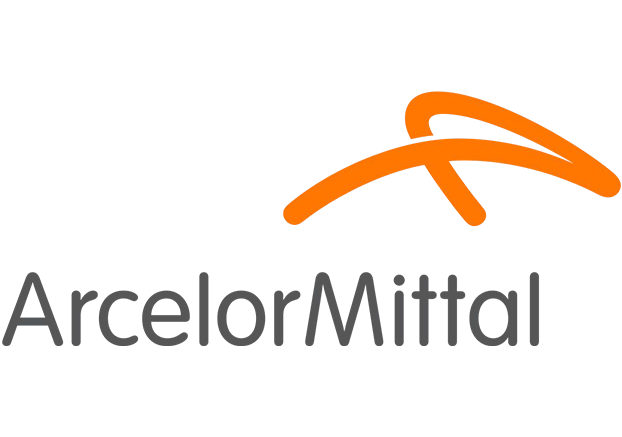
Case Study 9
DATE:
10/5/2019
ISSUE:
Bridgestone iTrack picked up a potential mechanical issue by monitoring the temperature delta of the 2 front tires
NOTIFICATION:
Bridgestone iTrack flagged the truck and informed the customer to inspect. This is reported on the daily dashboard report that is sent out to the customer each morning
ACTION:
An order was put in for the truck to be checked during PM for a tweaked frame and strut pressures on the next fuel top off. Bad right front strut confirmed and changed out.
WIN:
Picking up this issue in advance prevents major damage to the truck and lengthy downtime. Tires are more susceptible to cuts and premature wear which could result in shorter tire life by 25%-50% for multiple tires until problem resolved.
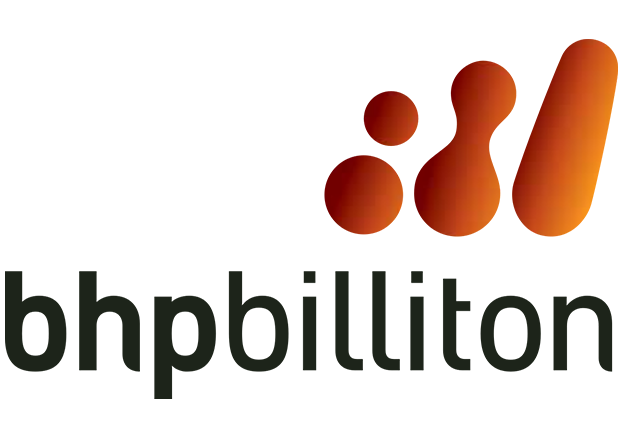
Case Study 10
DATE:
9/5/2019
ISSUE:
Through an analysis of Temperature Differences between positions 1 and 2 of the CEX12 truck, it was detected that position 1 (front right), was heated much more than position 2 (front left), with a difference of 15 ° C.
NOTIFICATION:
The tire maintenance area was notified and requested to check the truck suspensions.
ACTION:
The maintenance area detected that one of the rear suspensions was damaged. Then it was deduced that the truck was distributing the loads poorly and position 1 was carrying a greater amount of the load than position 2. The maintenance area made a change to the suspension and the temperature difference was reduced to 5 ° C.
WIN:
By reducing the temperature difference it follows that the load received by position 1 was reduced and the load at position 2 increased, generating a more equitable distribution of the loads. This will allow the tire of position 1 not to get so hot, and that all the forces in the tire decrease, increasing the life of the tire and reducing the chances of a tire blowout prematurely.
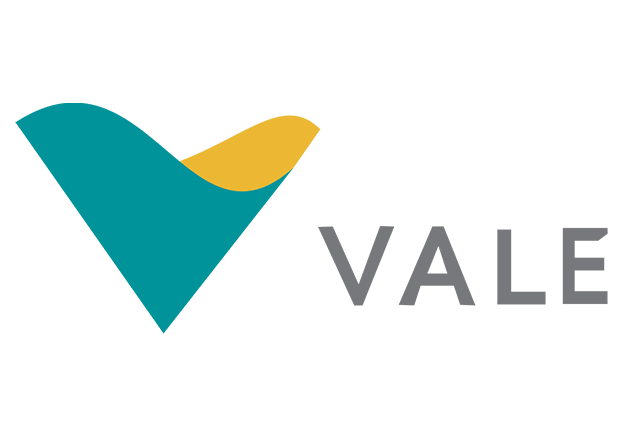
Case Study 11
DATE:
12/11/2019
ISSUE:
Truck CM1406 had a fast pressure leak in position 4, the tire reached a level 3 alert
NOTIFICATION:
Bridgestone iTrack contacted the mine and recommended that the crew inspect the tire and take the recommended corrective action
ACTION:
The maintenance crew stopped the vehicle and took it to maintenance where they discovered a puncture and repaired it.
WIN:
Tire saved approximately ~$40,000 depending on the residual tread depth and potentially its twinned tire too because of early intervention when a puncture occurred.
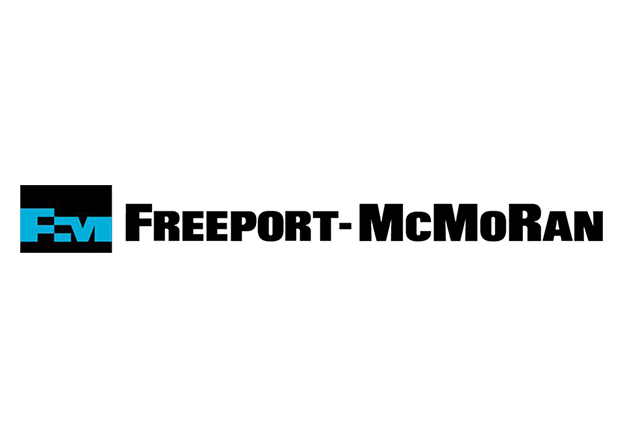
Case Study 12
DATE:
17/1/2020
ISSUE:
Truck 203 had a pressure leak in position 3, the tire reached a level 3 alert
NOTIFICATION:
The Bridgestone iTrack system sent an alert notification, also an email was sent from the monitoring center with the recommendation that the tire is inspected and corrective action taken.
ACTION:
The onsite tire crew inspected the vehicle and it was found that the tire had been cut.
WIN:
The tire was removed and was sent for repair
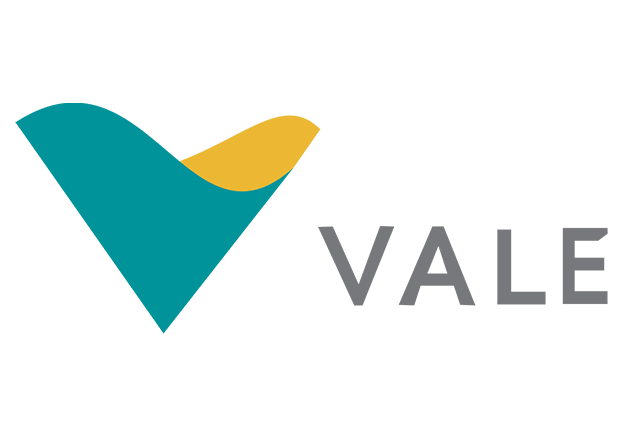
Case Study 13
DATE:
17/1/2020
ISSUE:
Truck CE1513 has a slow pressure leak in position 4. Currently, the tire is in a Level 3 Low-Pressure Alert
NOTIFICATION:
The Bridgestone iTrack system sent an alert notification, also an email was sent from the monitoring center with the recommendation that the tire is inspected and corrective action taken.
ACTION:
The truck was moved to the Maintenance Area for corrective maintenance.
WIN:
The tire crew was able to find the damage and make the repair, the tire was saved.
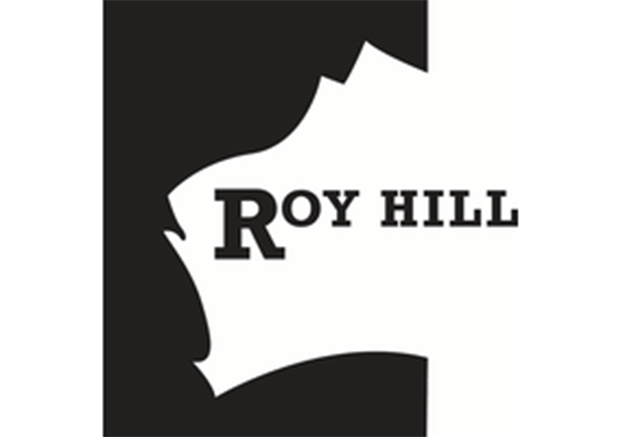
Case Study 14
DATE:
7/1/2020
ISSUE:
Truck DT076 had a pressure leak in position 6, the tire reached a level 3 alert
NOTIFICATION:
The Bridgestone iTrack system sent an alert notification, also an email was sent from the monitoring center with the recommendation that the tire be inspected and corrective action taken.
ACTION:
The onsite tire crew inspected the vehicle and it was found that the valve extension had been damaged
WIN:
Tire saved approximately ~$36,000. As this was a dual position the partner tire was also saved from damage.
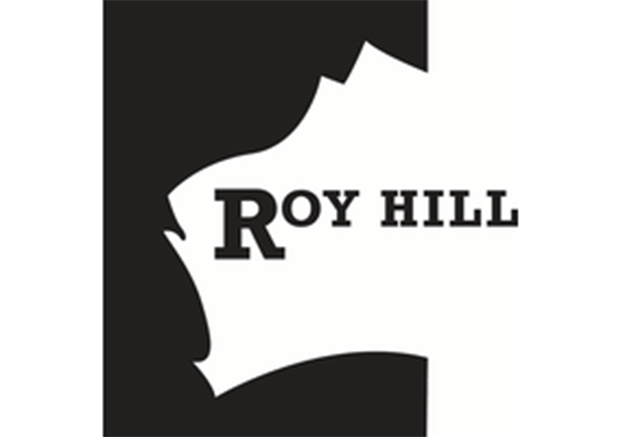
Case Study 15
DATE:
8/1/2020
ISSUE:
Truck DT058 had a pressure leak in position 6, the tire reached a level 3 alert
NOTIFICATION:
The Bridgestone iTrack system sent an alert notification, also an email was sent from the monitoring center with the recommendation that the tire is inspected and corrective action is taken.
ACTION:
The onsite tire crew inspected the vehicle and it was found that the valve extension had been damaged by the rock ejector chains. The valve was replaced, the chains were also shortened. The tire was saved.
WIN:
Tire saved approximately ~$21,000. As this was a dual position the partner tire was also saved from damage.
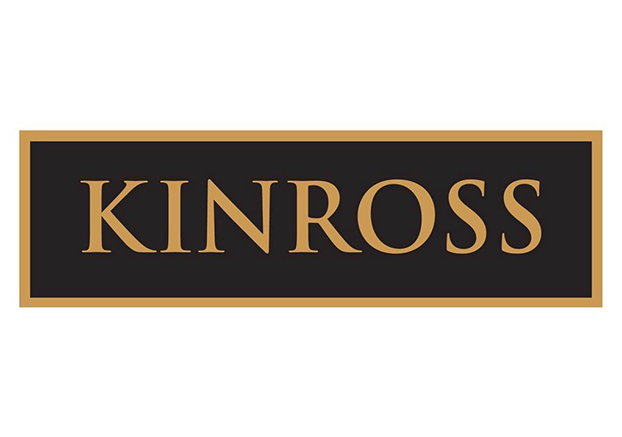
Case Study 16
DATE:
26/3/2020
ISSUE:
Truck HT803 position has a pressure leak. Currently, the tire is at Level 3 Alert
NOTIFICATION:
The Bridgestone iTrack system sent an alert notification, also an email was sent from the monitoring center with the recommendation that the tire is inspected and corrective action is taken.
ACTION:
The onsite tire crew inspected the vehicle and it was found that the valve extension had been damaged.
WIN:
This 57” tire had only done 1500 hrs and had 111 mm of tread remaining, the valve was replaced and the tire was saved.
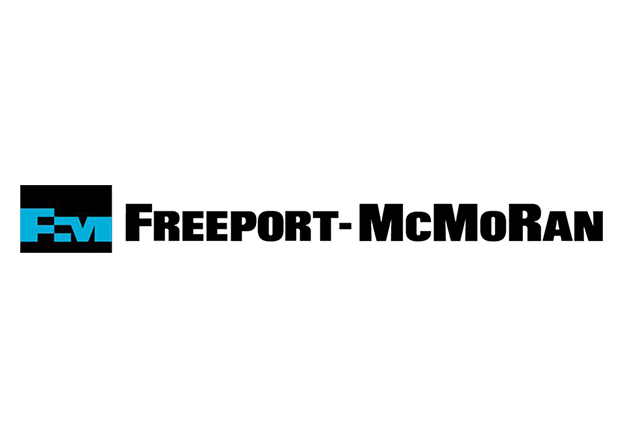
Case Study 17
DATE:
2/4/2020
ISSUE:
Truck 152 position 3 has a pressure leak. Currently, the tire is at Level 3 Alert. We recommend that you inspect the tire and take the recommended corrective action.
NOTIFICATION:
The Bridgestone iTrack system sent an alert notification, also an email was sent from the monitoring center with the recommendation that the tire is inspected and corrective action is taken.
ACTION:
Confirmed as a leak, truck heading back to the tire bay
WIN:
Tire saved approximately ~$21,000. As this was a dual position the partner tire was also saved from damage.
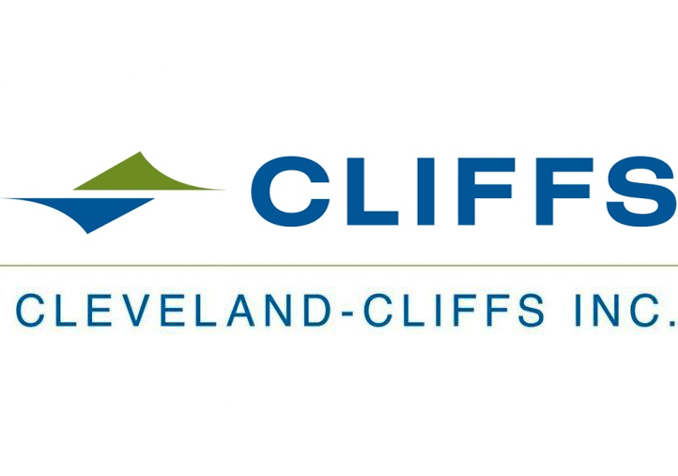
Case Study 18
DATE:
3/4/2020
ISSUE:
Truck 536 position5 has a pressure leak. Currently, the tire is at Level 3 Alert. We recommend that you inspect the tire and take the recommended corrective action
NOTIFICATION:
The Bridgestone iTrack system sent an alert notification, also an email was sent from the monitoring center with the recommendation that the tire is inspected and corrective action is taken.
ACTION:
“Good morning, We picked up the air loss on our cell phone before the control center seen it. The brakes were spiked and the rim spun on the hub and tore the inside valve stem off. We are fixing it as you read this.”
WIN:
The tire was saved by this system!